この記事の内容は、下記の質問にお答えしています。
- 一般構造用圧延鋼材とは? 溶接構造用鋼材とは?
- 圧延加工とは?
- H鋼やL型鋼の材質は?
- SS400特長とは?
- SM材、SN材、SS材の違いとは?
- SPCC材とSPHC材の違いについて、熱間圧延と冷間圧延ではどんな違いがあるのか解説
- 酸化皮膜の正体とは? 黒皮は、どのように形成されるの?
- めっき処理とは?
- ブラスト処理とは?
- ショット処理と酸洗の違いとは?
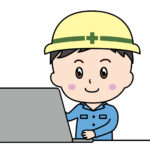
監督〜
今回は、鋼材の種類についての解説なんですね〜?
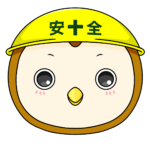
そうや〜
これまでの解説で紹介してきた材質があったけど、
今回の解説で、バコーンとまとめようと思うてな〜
それと、機械屋にとって必要な知識をコメントしていくつもりやで〜
鋼材とは、鋼のレンジやけど、炭素鋼と合金鋼に分かれてたと思うけど、
今回は、炭素鋼の種類と特徴を解説するで〜
それと、鋳鉄のレンジがあり、鋳鉄にも色々な材質があるから、
鋼材の種類(上・下)と、鋳鉄の種類の3回に分けて、解説するで〜
それと、圧延加工では、鋼材の表面に酸化皮膜ができるんやったな
その酸化皮膜の正体と、除去方法について解説するで〜
レベル1 一般構造用圧延鋼材
まずは、下記の図解からやな
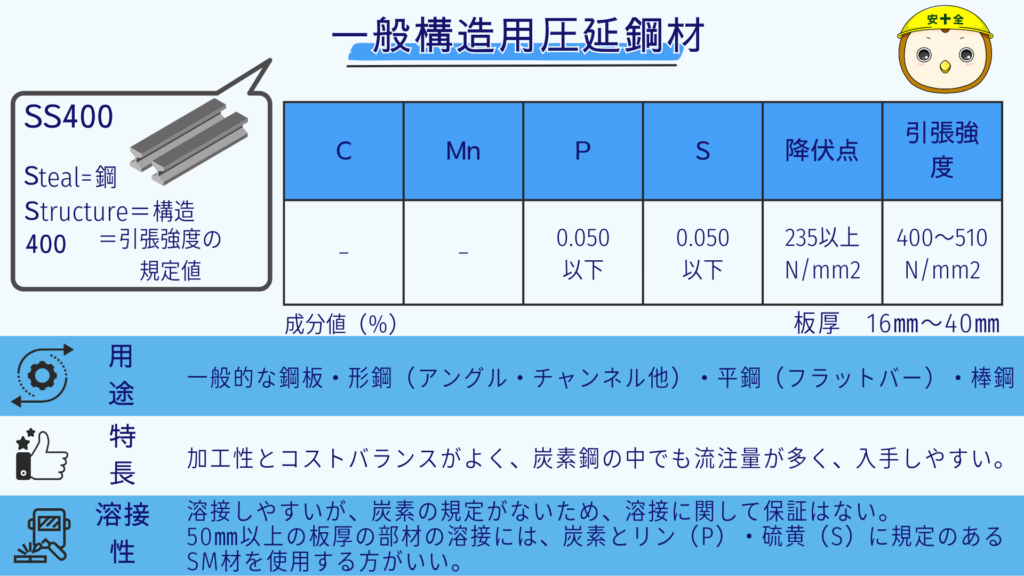
まずは、SS400から解説するで〜
一般的に最も使われている鋼材で、流通量が多く、入手しやすいとされてるんや!
俺たちが使う鋼材のほとんどが、このSS400やな、だから、一般構造と言うんや!
圧延鋼材とは、上下のロールで伸ばしていくんやったな! 下記の図解を参考にしてや〜
https://jp.meviy.misumi-ec.com/info/ja/archives/30701/
形鋼(鉄板 L型鋼 H型鋼 丸鋼 角鋼 鋼管)は、ほとんどが、SS400で、加工方法は、
圧延加工で、製造されてるんや
熱間圧延加工と冷間圧延加工があるんやけど、
違いは、熱間圧延は、900度から1200度に、銑鉄(ワーク)に熱を加えてから加工(伸ばす)するが、
冷間圧延は、常温の状態で、加工するんや
熱間圧延加工の表面は、加熱してからの加工やからな、表面が熱により酸化してしまうんや!
だからな〜 熱間圧延鋼材は、必ず、表面に酸化被膜ができるんや
酸化被膜とは、鋼材の表面にうっすらとした膜で、その黒い膜を、黒皮と言われるんやで〜
圧延加工に関しては、鉄の製造プロセスの記事に詳しく解説しているので、参考にして下さい。
話を戻すで〜
特徴は、炭素含有量の規定値はなく、リンと硫黄の規定値があるんや
SS材には、SS330、SS400、SS430、SS490、SS540があるんやけどな〜
それぞれ、引張強度の下限値が名称に入れられてるんや!
図解は、SS400やから、引張強度の下限値は、400N(N)と記載されてるんや!
同じ、SS400でも、板厚によって、降伏点が違ってくるのが違いやな
詳細は、下記やな(各板厚に対しての降伏点)
- 16㎜以下 降伏点 245N 以下
- 16㎜〜40㎜ 降伏点 235N 以下
- 40〜100㎜ 降伏点 215N 以下
- 100㎜以上 降伏点 201N 以下
重要な点は、成分で、SS材は、炭素の規定値がなく、リンや硫黄の規定値も若干甘めやな!
規定値が低い理由は、製造しやすいというメリットがあるんやな〜
炭素鋼の中でも低炭素鋼(0.3%以下)と高炭素鋼(0.3〜2.1%)に、
炭素含有量で、分けることができるんやけどな〜
SS400は、低炭素鋼=軟鋼と言われるんや
だから、焼入れ性は、悪く、溶接性も保証されてるわけではないんやな〜
炭素鋼の焼入れ性は、下記の記事をして下さい。
溶接性は、炭素含有量が規定されていない為、保証されていないので、
厚板のSS400を重要な機械フレームに使う場合は、溶接構造用鋼材を使う方がいいんやな!
溶接構造物は、割れとの戦いなんや〜
熱処理でも熱歪みと、焼き割れとの戦闘が起こっとるんやけどな〜
溶接割れに強い材質の研究の結果が、SM材なんやな! 次に解説するで〜
レベル2 溶接構造用圧延鋼材
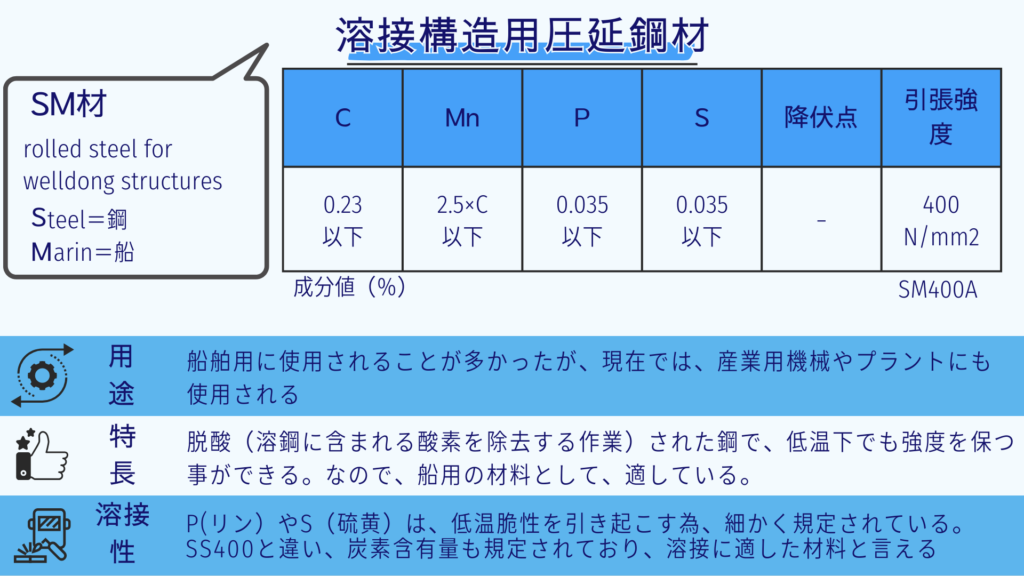
船舶は、溶接構造物の塊みたいなもんやろ〜
だからな! 造船には、SM材が使われるんや!
現在では、造船だけでなく、産業用機械やいろんなプラント建設にもSM材が使われてるんやで〜
第二次世界大戦の戦争時代、戦艦大和の時代や〜 その時の戦艦は、溶接構造物ではなく、
リベット構造やったんやで〜 どんな構造と言うとやな〜
http://blog.livedoor.jp/kouteisukedzf/archives/50664311.html
戦艦の上にいるのが、かしめ工の二人や! 戦艦のフレームは、鉄板と鉄板をかしめて固定してるんや
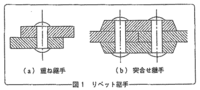
重ね合わせて固定する方法と、鉄板同士を突合せて、他の鉄板を重ねて固定する方法の組み合わせで、
戦艦は、建造されていたんやな〜
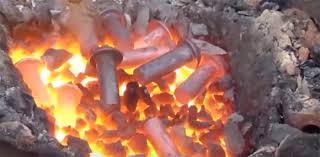
上の写真みたいに、ピンを加熱して、鉄板の穴を通して、先端をハンマーで潰して固定してるんや
もう必死のパッチで、大ハンマー振って打ち込んでいくんやな〜
このリベット式のデメリットは、鉄板を重ねる構造になるので、構造物の重量が重くなることや!
メリットは、溶接をしないので、割れの発生がないことやな
戦後の造船では、溶接用の鋼材が開発されたことと、溶接材料の開発が進んだことで、
現在の造船では、溶接構造が採用され、SM材が使われてるんや
SM材が、溶接構造に強い特徴は、炭素の含有量が厳しく規定してあるのと、
リンと硫黄も規定されてることや、リンと硫黄の含有量が多いと強い鉄にならないんやで〜
炭素含有量が多いと、熱影響を受けまくるので、割れの発生リスクがマックスになるんやったな!
SM材の種類は、11種類あるんや
SM400A SM400B SM400C SM490B SM490C SM490YA SM490YB SM520B SM520B SM520C SM570
400の記載は、引張強度で、Aとは、A種と言われて、耐候性に強い材料という意味や
耐候性とは、熱や紫外線、雨水などに抵抗できるように設計されてるんや
BとCの意味は、B種とC種と呼ばれれ、耐衝撃に強いとされているんや
SM材には、シャルピーの衝撃値の規定があるんや! B種より、C種の方が強いという意味やで〜
シャルピーの衝撃値に関しては、下記の記事を参考にして下さい。
あと、SN材もあるんやけどな〜 これは、建設構造用圧延鋼材や
日本では、昔から地震が多くてな、1970年〜80年代には、地震で橋の梁や建設構造物が崩壊したりと
ここでも、溶接構造物の溶接割れの問題との格闘があったんやな〜
だから、SN材は、SS材やSM材より、引張負荷が原因の溶接部の脆性破壊が起こりにくい特徴があり、
高い耐震性を持っているのが特徴なんやで〜
要は、地震に負けない溶接強度を持てるようにしとんやな〜
やはり、SN材も炭素含有量の規定値とリンと硫黄の厳しい規定値があるんや
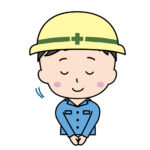
監督〜
SS材、SM材 完全に理解しました〜
今まで、SS400しか知らなかったんですが、溶接構造用の材質が
あったんですね。
鋼材編の知識があったから、理解が完璧でした
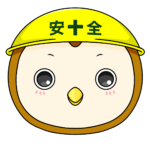
今回のSS材、SM材、SN材の解説で、
俺が本当に伝えたかったんは、
溶接構造物の溶接割れは、昔からあった事と、そこには、必死のパッチの格闘が
あったちゅう事を言いたかったわけよ〜
戦後の造船現場で、大震災を何度も何度も経験した建設現場ではな〜
溶接割れとのバッチバッチの戦闘やったと思うで〜
そんな、先輩方の経験を理解することは、機械屋にとっては、
めっちゃ重要なことで、現在でも起こっている溶接割れに対抗する為のヒントが
そこにはあると、俺は思っとるんや!
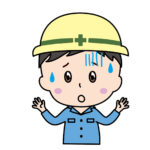
わかりました。
昔の経験があることで、現在では、良い材質が開発されて、
我々の現場でも安全が担保されてるんですね〜
その経験と知識があれば、現在でも起こっている溶接割れを回避できるんですね。
だから、監督は、必死のパッチで解説してるんですね〜
やはり、溶接すると、母材(鉄)が、熱影響を受けるんですね?
そうすると、歪みが出るし、脆性破壊が起こるんですね?
(脆くなる)のですね?
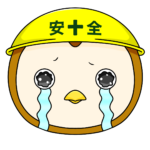
その通りやで〜
やりよるな 組立君!
溶接に関しては、次回以降の解説になるんやけどな〜
重要なポイントではあるので、レベル上げていこうか〜
次は、SPC材の解説、いくで〜
レベル3 冷間圧延鋼板
炭素鋼の最後は、冷間圧延鋼板や、図解は、下記やで〜
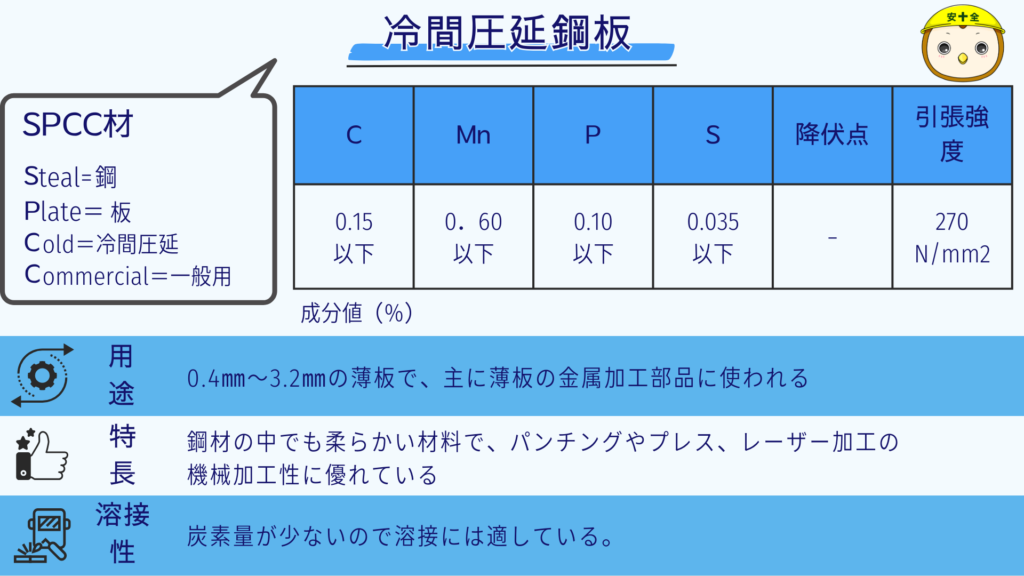
冷間圧延鋼板は、SS400に比べて、炭素含有量が少ないので、硬度も低いし
引張強度も低く設計されているんや! それに炭素含有量が少なく、溶接性もいいんや!
強度を落としている理由は、曲げ加工やプレス加工が簡単になる=機械加工性を上げてるんや!
用途としては、薄物の機械部品や機械のカバーなどに使われてるんや
強度の必要な部品には、同じ厚みの仕様でも、SS400が採用されることがあるんや
要は、薄いし、弱いので、簡単に曲げて、切り落として、加工できるんや
冷間圧延鋼板は、常温で圧延加工するので、酸化被膜がなく、光沢がある綺麗な表面を
してるんやで〜
SPHC材もあってな、熱間圧延鋼材のことやで〜 H=熱間 C=冷間の意味やな
熱間圧延鋼板は、酸化被膜ができてしますので、表面は、黒皮があり、光沢がないんや
冷間圧延鋼板(SPCC)と熱間圧延鋼板(SPHC)を比較して、まとめると、下記になるんや
SPCC(冷間圧延鋼材) VS SPHC(熱間圧延鋼材)
- 加工温度 常温 900度〜1200度
- 加工の難度 難しい 易しい
- 寸法精度 良い 悪い
- 表面 光沢があり綺麗 酸化被膜あり
- 加工後の熱処理 必要 不要
- 名称 ミガキ 黒皮
熱間圧延は、900度以上に加熱するので、加工は易しいが、熱膨張するので、寸法精度が落ちるし
表面に酸化被膜ができてしまうんや
冷間圧延は、加熱しないので、加工=引き伸ばすのが困難なんや!
その代わりに寸法精度が良いのと、表面に光沢があるんや!
デメリットは、加工に時間を必要として、引き伸ばす加工の頻度や力も多く必要とするんや
ゆっくる伸ばさないと伸びないので、何度も何度も少しずつ引き伸ばしていくので、
加工硬化してしまい、脆くなるんや!
加工硬化とは、加工途中で硬化してしまうことや、硬くなるっちゅうことは、脆くなることやったな!
例えば、針金を切るときに、同じところを何度もクネクネして折り曲げると、ホキっと折れたとき
あるやろ〜! クネクネが、加工とイコールとして、ホキっと折れるのが、
硬化 → 脆性(脆くなること)やな!
冷間圧延は、加工途中で、硬くなるので、硬くなった代わりに脆くなっているので、
焼きなまし(熱処理)をして、靭性のある強い鋼材にする必要があるんや、だから、
冷間圧延鋼材には、熱処理(焼きなまし)が必要になるんや
最後に、冷間圧延は、光沢がある表面なので、ミガキとも言われるんや、磨いてるみたいに
綺麗やからな〜、熱間圧延は、黒い皮(酸化皮膜)があるので、黒皮って言われるんや
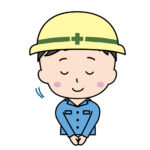
監督〜
SPC材、理解しました〜
SPCC材とSPHC材の違いも理解できました。
先輩から黒皮とか、ミガキとかって聞いていましが、
意味がわかりませんでした〜
今回の解説で理解できました。
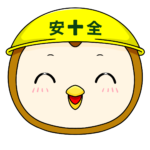
製鉄所で圧延鋼材と言われてる鉄板や型鋼は、熱間圧延で加工されてるので、
酸化被膜があるんやで〜
しかし、黒皮がなく光沢があるニーズには、薄板に限るが、
SPCC材(冷間圧延材)があるんや
ここ重要なポイントなんやけどな、酸化被膜があれば、錆や腐食に強いんやけど
ミガキ材は、錆には弱いんやで〜
だけどな〜、SPCC材は、表面処理して、違う材質に生まれ変わるんや!
次に、表面処理についての解説いくで〜
レベル4 表面処理(めっき処理)
下の缶もSPC材からできてるんやで〜
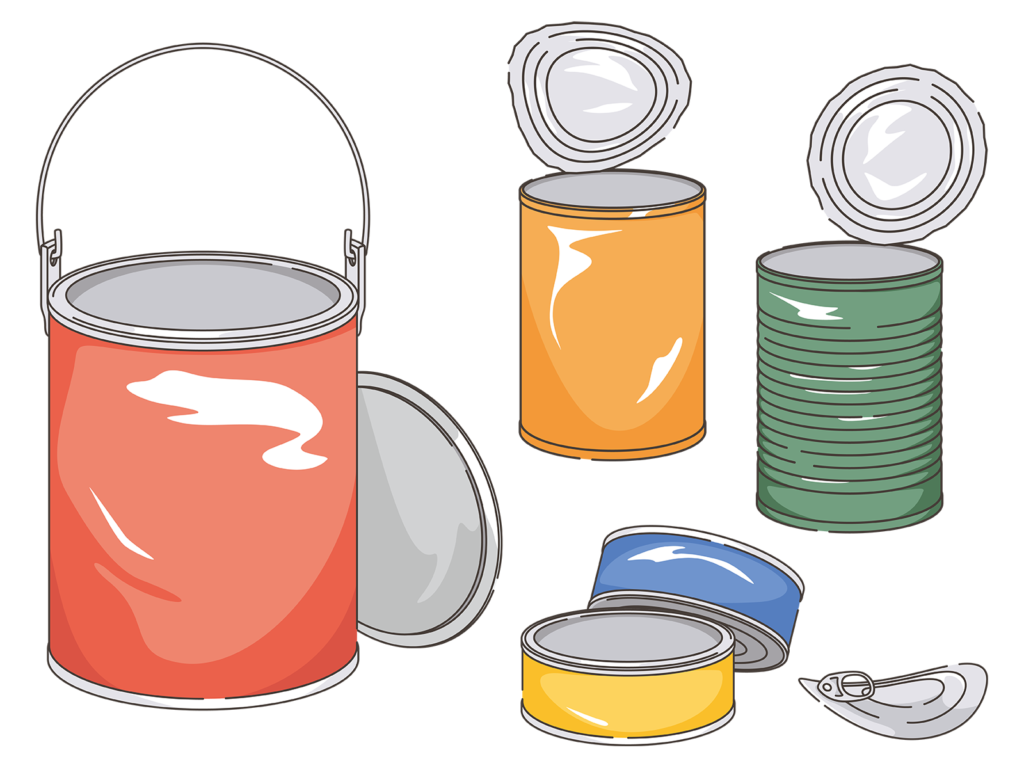
オイル缶や塗料缶、食品が入っている缶には、SPC材が採用されてるんや!
多くは、SPCC材(冷間圧延)に、表面処理してるんや、
SPHC材に表面処理したものもあるんやで〜
缶の内側は、キラキラした光沢があり、綺麗に見えるけどな〜
あれは、圧延で引き延ばした薄鉄板に、スズをめっき処理したものなんや!
めっきとは、母材の金属の表面に、違う金属を成膜させる技術の総称のことや
スズは、沸点が低いので、溶かしたスズを塗布することで
昔からめっき処理が行われてたんやで〜
今では、めっき金属には、スズ、クロム、金、ニッケルがあり、
現在では、電気めっきが行われてるんやけど、電気分解を使って、めっき金属を
母材の金属に成膜させているんや!
SPC材にめっき処理を行った金属は、「ぶりき」って言われるんやけど、
ぶりきのおもちゃとか言われてる、それやな〜
今では、ぶりきの種類は、いろいろあるけど、機械ではあまり使われないので、
種類についての解説はここまでとしとくで〜 めっき処理は、ボルトの表面処理に使われているので、
レベル上げてから、また解説にするで〜
めっき処理の目的をまとめると、こんな感じや
- 耐食性 「防錆めっき」とも言われれ、材料を錆から保護する為に行われる
- 装飾性 「装飾めっき」と言われ、エンブレムや家電の装飾に使われる
- 機能めっき 「機能めっき」と言われ、電子部品などの電気的機能を与えるために行われる
次に、黒皮の酸化被膜がある鋼材の表面処理について解説するで〜
レベル5 ブラスト処理
酸化被膜(黒皮)の正体は、鉄が酸化しているので、錆の一種なんや
母材の表面を覆っているので、酸化や腐食の予防になってはいるが、酸化被膜は、剥がれやすかったり、
被膜内部には、小さな穴が開いてるんやで〜なので、やはり、母材も錆びていくんや
酸化被膜は、塗装や溶接するときは、邪魔な存在でもあるんや〜
酸化被膜の上から塗装するとやな〜
酸化被膜と一緒に、せっかく塗った塗装が剥がれてしまうんや
まあ、すぐ剥がれるんやなくて、長持ちしなくなるっちゅう程度やけどな〜
なので、表面処理が必要になるんやで〜
イメージは、下記の図解やな〜
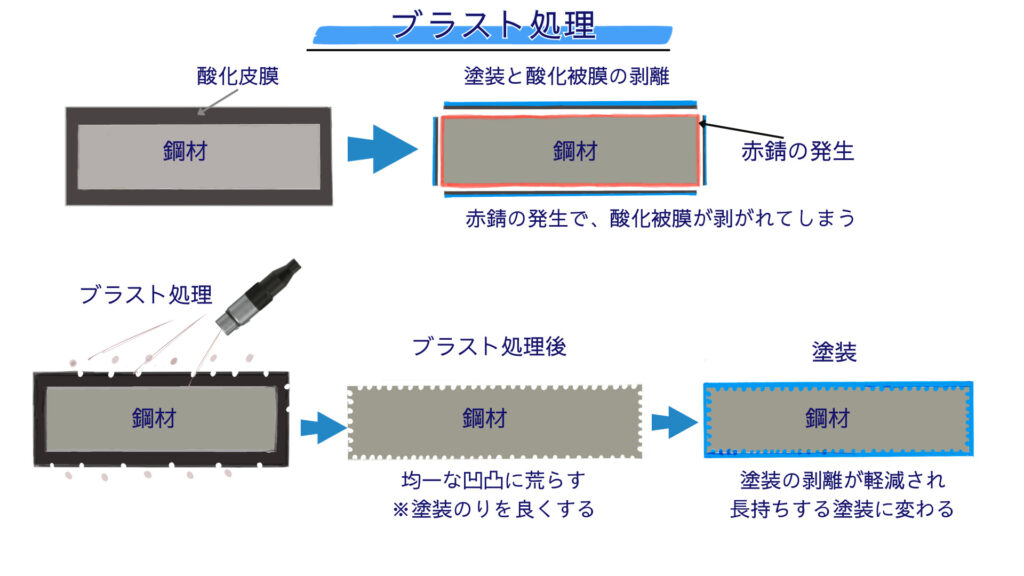
それが、ブラスト処理や! イメージは、上記図解の下の部分やで〜
ブラストの設備概要は、こんなイメージや
https://saitama-yuuwa.com/blasting/
サンドブラストもあるんやけど、同じブラスト処理の1つや
要は、加工物に、ぶつける物(投射剤)によって呼び名が違うだけやで〜
投射剤には、下記があるんや
- 鋼鉄製/鋳鉄製の小球(ショット)
- 小さな砂(サンド)
- ガラスビーズ
処理前と処理後の画像を見てみると、下記の写真やで
https://kamiita.co.jp/facility/formar1.html
ブラスト処理の目的は、酸化皮膜の除去と清掃、母材の表面を荒らすことにあるんや!
要は、品物の表面を凸凹に、なるべく均一に凸凹にすることで、塗装のりがよくなるんや
塗装のりが良くなることで、長持ちするんや、化粧の下塗り=下地処理と一緒やな〜
皮脂や油、汚れを除去することで、化粧のりも良くなるっちゅうことや!
手動で行う場合と自動設備があるんや
図解では、下記のイメージやで〜
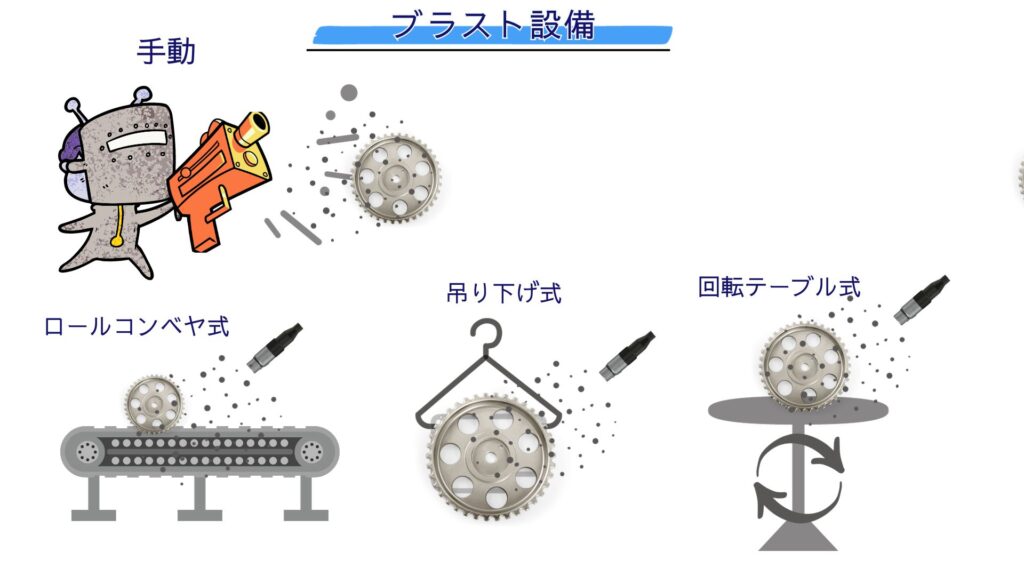
手動は、品物に水で放水するような感じで、水の代わりに、ショット剤(投射剤)を、吹き付ける
ことで、品物の表面の錆や汚れ、酸化被膜を除去するんや!
自動設備は、ロールコンベヤ上で、吹きつけたり、ハンガーに吊り下げて行ったり、
回転テーブル上で、吹き付ける場合があるんや
満遍なく、均一に吹き付けたいけどな〜、難しい場合があるんや
複雑な形状やったりすると、細かい窪みや、奥ばった形状では、ショットが届き難い場合が
あるんや〜、その時は、酸洗が必要になるんや!
酸洗とは、酸の入ったプールに品物をつけることで、化学反応によって、酸化皮膜を除去する方法や
ショットブラストが物理的な除去方法なら、酸洗は、化学的な除去方法と言えるわな〜
溶接の場合では、酸化被膜は、やはり邪魔者になるんや
酸化被膜は、錆の一種と説明したけど、普通の錆を赤錆とするなら、酸化被膜は、黒錆って言われるんや
錆びている鋼材に、溶接するとやな〜、正常なビードが形成できずに、弱い溶接になってまうねん!
溶接ビードの中に、不純物(錆)入ってしまうので、弱い溶接になってしまうんや
溶接の種類によっては、必ず除去しなければいけない場合もあるくらいやけど、
詳しい話は、溶接の解説の後にするで〜、楽しみにしといてや〜
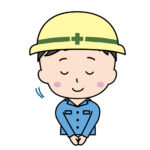
酸化皮膜の正体は、錆だったんですね〜
知りませんでした。
溶接や塗装の前に、「黒皮を剥げ」って言われたことありましたが、
酸化皮膜が邪魔者になってたからねんですね〜
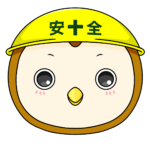
その通りやで〜
溶接や塗装前の一手間が必要なんやな〜
SPCC剤のめっき処理も同じことで、酸化皮膜があると、めっき処理が
できないから、酸化被膜がない冷間圧延材が使われているんや
SPHC材(熱間圧延)を使う場合は、酸化皮膜の除去が必要なんや
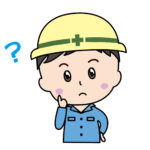
そうなんですね〜
ドラム缶やペール缶はよく見かけますが、内側の光沢は、
めっき処理されたスズやニッケル、クロムだったんですね。
質問があります〜!
めっき処理のめっきは、なぜ、ひらがななんですか?
外来語の「メッキ」と思っていました。
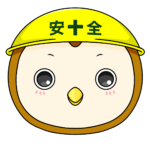
めっきを漢字で書くと、これやで〜、鍍金(めっき、ときん)
鍍金とは、金属に他の金属を固着させることなんや
要は、昔から日本にあった表面処理技術やな〜
塗装や溶接に関しては、それぞれ詳しく解説するので、楽しみにしといてや〜
次は、合金鋼材の解説やで〜 炭素鋼との比べてみよう!